Kaizen is a straight forward but effective Japanese idea that promotes ongoing development for both people and companies. It demonstrates how minor adjustments performed regularly over an extended period of time can result in major advancements. Kaizen is a tool used by businesses all around the world to increase output, cut waste, and boost quality. We’ll discuss what Kaizen is, its tenets, or “Kaizen codes,” and how they promote ongoing development in this blog. We’ll also go over the advantages of earning a Kaizen certification online to assist you in becoming proficient in these effective methods.
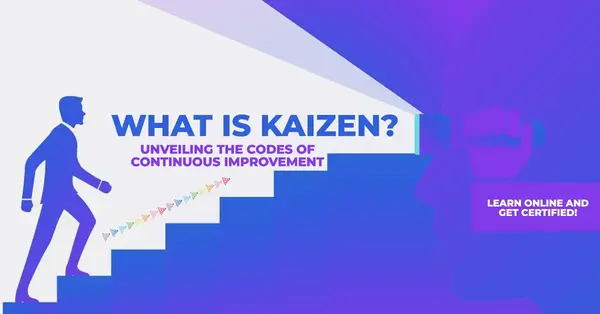
Kaizen: What Is It?
Kaizen is a compound word made up of the Japanese terms “Kai,” which means change, and “Zen,” which means good. When combined, they mean “change for the better.” Fundamentally, kaizen refers to the steps done to guarantee ongoing progress. After World War II, Kaizen emerged in Japan and was crucial to the country’s economic recovery. Toyota, one of the businesses that popularized this idea, consistently made tiny but significant adjustments, which led to tremendous advances in efficiency and quality.
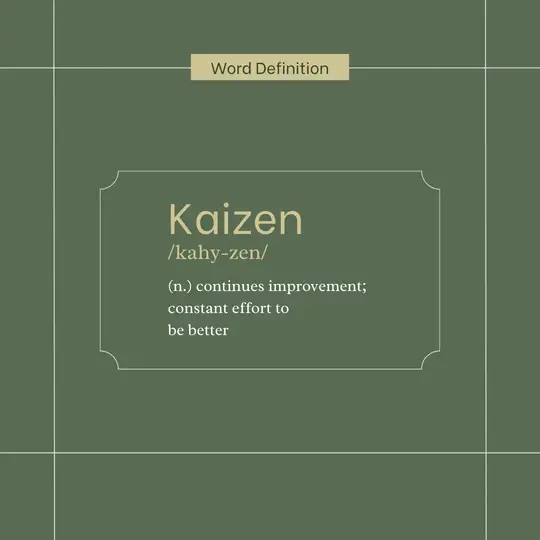
Kaizen focuses on gradual, tiny changes that add up over time as opposed to abrupt, large overhauls. In both the professional and personal spheres, Kaizen encourages an attitude of continuous improvement and self-evaluation. Kaizen improves teamwork, increases employee engagement, and produces long-term success in enterprises. It promotes everyday self-improvement, which fosters personal growth in individuals.
Recognizing Kaizen’s True Significance
Kaizen is all about making constant improvements in both personal and professional spheres. It promotes collaboration between managers and staff to make small, continuous improvements in the workplace without the need for additional funding or incentives. Over time, these little adjustments become ingrained in the daily routine, increasing productivity and producing superior outcomes.
Kaizen encourages staff members to point out inefficiencies and make suggestions for improvements, so fostering a culture of continuous improvement in enterprises. Better products, quicker delivery, and lower costs are the end results of this, which eventually raises consumer happiness. It fosters personal development by giving people the opportunity to share their thoughts and strengthen team dynamics.
Kaizen prioritizes continuous improvement above short-term remedies in favor of long-term fixes. In the fast-paced global market of today, businesses can maintain their competitiveness by constantly looking for methods to improve. The Japanese concept of kaizen emphasizes gradual, steady improvements over abrupt changes, which emphasizes the value of persistence, attention to detail, and long-term planning.
For instance, if you make 1% improvement every day for a year, you would have improved 37 times at the end of the year. This is a potent illustration of the compounding effect of tiny adjustments, as James Clear emphasizes in his book Atomic Habits.
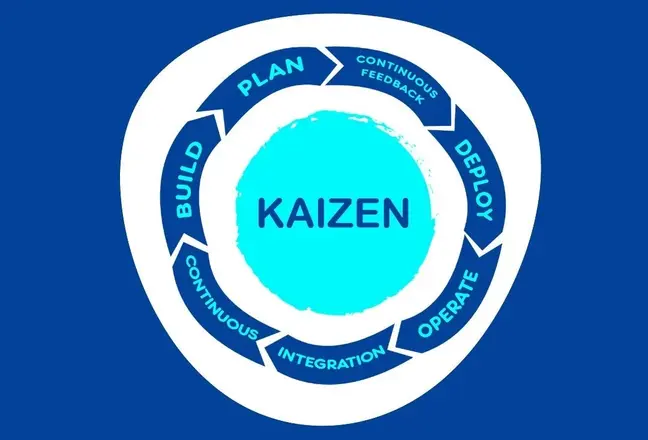
Kaizen in Various Situations
1. Enterprise
Kaizen is the practice of continual improvement in company that involves workers at all levels, from executives to manufacturing workers. Increasing output, effectiveness, and quality is the aim.
As an illustration, a maker of smartphones welcomes daily employee comments for enhancements. One employee discovers that the time it takes to assemble a phone can be decreased by rearranging the tools on the production line. Over time, although being a minor adjustment, it results in considerable increases in production.
2. Production
Kaizen and manufacturing go hand in hand, especially with the Toyota Production System. Its main objectives are to reduce waste, enhance procedures, and involve staff members in problem-solving.
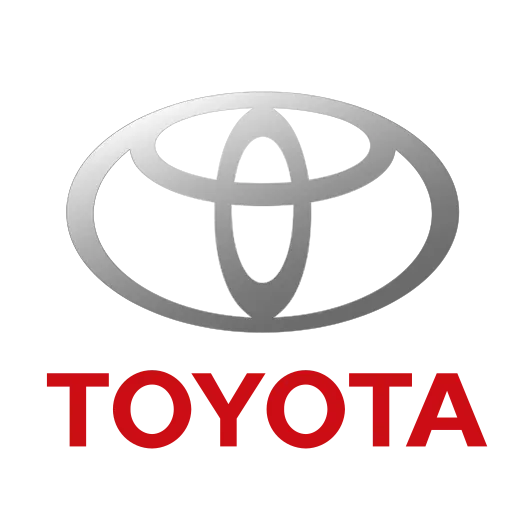
Example: Employees at an auto industry may recommend minor changes to a procedure that is causing delays. The business can cut expenses and manufacturing time by putting these suggestions into practice.
3. Individual Development
Applying kaizen to personal growth means making gradual, manageable adjustments to enhance relationships, abilities, health, and other aspects of life.
Example: A 5-minute daily stroll could be a good place for someone trying to get fitter to start. This gradual adjustment is less overwhelming and more maintainable than a major overhaul because they can increase the duration and intensity over time.
Continuous, Long-Term Reform vs Snap Fixes
Kaizen prioritizes sustainable, long-term progress above band-aid solutions. Steady, gradual adjustments are easier to manage and maintain than abrupt, radical ones. This is the reason why:
- Sustainability: Quick fixes often provide immediate results but may not last. Small, continuous improvements are easier to maintain over time.
- Engagement: When everyone is involved in the process of improvement, there’s greater engagement and a sense of ownership over the changes.
- Adaptability: Continuous improvement fosters flexibility and adaptability, helping organizations and individuals respond more effectively to challenges.
Understanding Kaizen Codes
The fundamental ideas that underpin continual improvement are known as kaizen codes. These guidelines guarantee the slow, steady advancement that Kaizen encourages. Now let’s explore the important Kaizen codes:
- Teamwork: All staff members, from front-line workers to management, must collaborate in order for each member’s insights to be used to improve procedures.
Example: Toyota’s “Kaizen blitz” meetings promote group conversations to swiftly resolve issues.
- Self-discipline: Kaizen encourages accountability and self-control. Instead of waiting for orders, employees actively monitor and improve their work.
Example: factory workers ensure the caliber of their work by identifying and fixing mistakes before they become more serious.
- Quality Circles: Small groups of workers gather regularly to discuss specific difficulties and provide solutions.
Example: Canon’s quality circles maximize productivity at workstations by proposing minor changes to the arrangement of tools.
- Continuous Improvement: This is the foundation of Kaizen; little, gradual advancements add up over time to produce significant results.
Example: Nissan is constantly improving the efficiency of its assembly line to produce cars without completely revamping the system.
- Waste Reduction (Muda Elimination): Waste Reduction (Muda Elimination): Kaizen focuses on getting rid of extraneous materials, time, or energy from processes.
Example: Streamlining the flow of commodities, for instance, lowers waste and increases efficiency in logistics.
Implementing the Kaizen Program
Businesses must adhere to the PDCA cycle (Plan, Do, Check, Act) in order to adopt Kaizen:
• Plan: Determine what needs to be improved upon and draft a thorough plan.
• Do: Put the plan to the test in a safe setting.
• Verify: Examine the outcomes and determine whether a wider implementation of the modification is necessary.
• Take Action: Standardize and implement the effective change throughout the entire organization.
Along with emphasizing waste reduction, kaizen also encompasses techniques such as 5S Kaizen (Sort, Set in Order, Shine, Standardize, Sustain), which guarantees that workspaces are set up for optimal productivity.
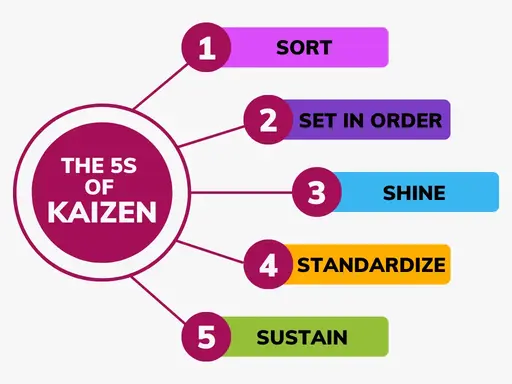
Advantages of Including Kaizen
Through its emphasis on ongoing enhancement, Kaizen offers businesses various advantages:
• Process Standardization: Reduces variation and inefficiency by creating standardized procedures.
• Waste Reduction: This process finds and gets rid of waste in any form, which makes operations leaner.
• Innovation: Encourages regular proposals for improvements, fostering innovation.
• Cost Savings: Productivity can be increased without significant investments by making little, gradual changes.
How to Get Expertise in Kaizen
To become a Kaizen expert, start by understanding its fundamental principles, such constant improvement and minimizing waste, through online classes or Lean technique books. Online certification programs for Kaizen are a great way to gain a thorough understanding of these ideas. They address Six Sigma, Lean techniques, and successful change management, which makes them perfect for anyone trying to improve their ability to implement ongoing, constructive changes at their place of employment.
The comprehensive course offered by ExpertRating’s Kaizen Certification Online is meant to teach you everything there is to know about Kaizen. It seeks to enhance your ability to implement Kaizen in your company, which will result in increased productivity and an ever-improving culture.
The course provides in-depth instruction on the definition, objectives, and applications of Kaizen in business. The course is suitable for beginners and culminates in an online certification exam. It complies with ISO 9001-2015 requirements, guaranteeing international recognition.
Selecting this certification is beneficial to your career because it is reasonably priced and demonstrates to potential employers your proficiency in streamlining corporate operations. Also, a lot of large corporations respect this accreditation. Because of its emphasis on practical skills, you may immediately apply what you learn to your line of work.
This credential may be quite helpful if you’re interested in improving your profession by gaining useful improvement abilities. It establishes your vital abilities and increases your employability in a variety of positions.
Advantages for Organizations and Professionals
Acquiring a Kaizen certification has substantial advantages for professionals and companies alike. Professionals can increase their skill set and become more valuable assets to their company by using this organized approach to problem-solving and process development. The accreditation can help organizations create a culture of continuous improvement, which will boost productivity, cut down on waste, and enhance overall performance.
Several essential characteristics are provided by the ER Kaizen Certification program:
Extensive Curriculum: Participants will receive a comprehensive understanding of continuous improvement processes as the curriculum covers key Kaizen principles, tools, and methodologies.
Flexible Learning: Working professionals will find the online format useful as it allows them to learn at their own speed.
Practical Application: To assist participants in implementing Kaizen techniques in their workplace, the certification includes hands-on activities and real-world examples.
Professional Growth: Earning a Kaizen certification can enhance career prospects by demonstrating a commitment to continuous improvement and operational excellence.
Impact on Organization: Qualified individuals are capable of spearheading Kaizen projects inside their companies, resulting in notable enhancements to workflow and output.
Conclusion
Kaizen empowers both individuals and organizations to pursue excellence through continuous improvement. It’s more than just a method; it’s a mindset. By applying Kaizen codes, you can drive significant improvements in efficiency, quality, and customer satisfaction.
Are you ready to enhance your career and foster continuous improvement in your organization? Sign up for the ExpertRating Kaizen Certification Online today to begin your journey toward becoming a Kaizen expert.
Conclusion
Kaizen gives individuals and organizations the tools they need to continuously improve and strive for excellence. It’s a mindset as much as a technique. You may significantly increase productivity, quality, and customer satisfaction by implementing Kaizen codes.
Are you prepared to advance professionally and promote ongoing development within your company? Enroll in the ExpertRating Kaizen Certification Online course right now to start your path to becoming a Kaizen expert.